Introduktion til tryktætningsventiler
Tryktætningsventiler
Tryktætningskonstruktion anvendes til ventiler til højtryksservice, typisk over 170 bar. Det unikke ved tryktætningens motorhjelm er, at forseglingen af krop-hjelmsamlinger forbedres, efterhånden som det indvendige tryk i ventilen øges, sammenlignet med andre konstruktioner, hvor stigningen i indvendigt tryk har tendens til at skabe utætheder i karrosseri-hjelmsamlingen.
Tryktætningsdesign
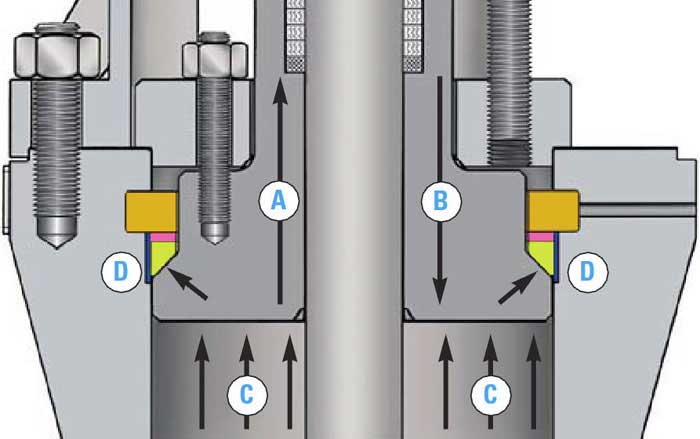
- A/B – Motorhjelmens tendens til at bevæge sig op eller ned, når trykket ændres
- C – Systemtryk
- D – Tætningskræfter på grund af tryk
Jo højere indre tryk, jo større er tætningskraften. Nem demontering er gjort mulig ved at slippe motorhjelmen ned i kropshulrummet og uddrive de fire-segmenterede trykringe ved hjælp af en trykstift.
Ved at stole på ret enkle designprincipper har tryktætningsventiler bevist deres evne til at håndtere stadigt mere krævende fossile og kombinerede dampisoleringsapplikationer, efterhånden som designere fortsætter med at skubbe kedel-, HRSG- og rørsystems tryk/temperaturkonvolutter. Tryktætningsventiler er typisk tilgængelige i størrelsesintervaller fra 2 tommer til 24 tommer og ASME B16.34 trykklasser fra #600 til #2500, selvom nogle producenter kan imødekomme behovet for større diametre og højere klassificeringer til specielle applikationer.
Tryktætningsventiler fås i mange materialekvaliteter såsom A105 smedet og Gr.WCB støbt, legering F22 smedet og Gr.WC9 støbt; F11 smedet og Gr.WC6 støbt, austenitisk rustfrit F316 smedet og Gr.CF8M støbt; til over 500°C, F316H smedet og egnede austenitiske støbekvaliteter.
Tryktætningsdesignkonceptet kan spores tilbage til midten af 1900-tallet, hvor ventilproducenter, stillet over for stadigt stigende tryk og temperaturer (primært i kraftapplikationer), begyndte at designe alternativer til den traditionelle boltede motorhjelm tilgang til tætning af karrosseri/kappesamlingen . Ud over at give et højere niveau af trykgrænsetætningsintegritet vejede mange af tryktætningsventildesignerne betydeligt mindre end deres boltede motorhjelmventil-modstykker.
Boltede hætter vs. tryktætninger
For bedre at forstå tryktætningsdesignkonceptet, lad os sammenligne krop-til-kappe-tætningsmekanismen mellem boltede hætter og tryktætninger.Fig. 1viser den typiske Bolted Bonnet-ventil. Kropsflangen og motorhjelmflangen er forbundet med tappe og møtrikker, med en pakning af passende design/materiale indsat mellem flangefladerne for at lette tætningen. Bolte/møtrikker/bolte spændes til foreskrevne momenter i et mønster defineret af producenten for at påvirke optimal tætning. Men efterhånden som systemtrykket stiger, øges risikoen for lækage gennem karosseriet/hjelmen også.
Lad os nu se på tryktætningssamlingen beskrevet i detaljerFig. 2Bemærk forskellene i de respektive konfigurationer af karrosseri/hjelmled. De fleste tryktætningsdesigns inkorporerer "hætteoptagsbolte" til at trække motorhjelmen op og tætne mod tryktætningspakningen. Dette skaber igen en tætning mellem pakningen og den indre dia (ID) af ventilhuset.


En segmenteret trykring fastholder belastningen. Skønheden ved tryktætningsdesignet er, at efterhånden som systemtrykket stiger, stiger belastningen på motorhjelmen og tilsvarende tryktætningspakningen. Derfor, i tryktætningsventiler, da systemtrykket stiger, falder potentialet for lækage gennem krop/hjelmsamlingen.
Denne designtilgang har klare fordele i forhold til boltede motorhjelmventiler i hoveddamp, fødevand, turbine-bypass og andre kraftværkssystemer, der kræver ventiler, der kan håndtere de udfordringer, der er forbundet med højtryks- og temperaturapplikationer.
Men i årenes løb, efterhånden som driftstrykket/temperaturerne steg, og med fremkomsten af spidsbelastningsanlæg, spillede det samme transiente systemtryk, som hjalp med tætningen, også kaos for tætningsforbindelsens integritet.
Tryktætningspakninger
En af de primære komponenter involveret i tætning af tryktætningsventilen er selve pakningen. Tidlige tryktætningspakninger blev fremstillet af jern eller blødt stål. Disse pakninger blev efterfølgende forsølvet for at drage fordel af det blødere pletteringsmateriales evne til at give en tættere forsegling. På grund af det tryk, der blev påført under ventilens hydrotest, blev der taget et "sæt" (eller deformation af pakningsprofilen) mellem motorhjelmen og pakningen. På grund af den iboende motorhjelmoptagningsbolt og trykforseglingssamlingens elasticitet eksisterede potentialet for, at motorhjelmen kunne bevæge sig og knække det "sæt", når det udsættes for systemtrykstigninger/-fald, med lækage af karrosseri-/hjelmleddet til følge.
Dette problem kunne effektivt afhjælpes ved at bruge praksis med "varmt tilspænding" af motorhjelmoptagningsboltene efter systemtryk og temperaturudligning, men det krævede, at ejeren/brugerens vedligeholdelsespersonale gjorde det efter anlæggets opstart. Hvis denne praksis ikke blev overholdt, var der mulighed for lækage gennem karosseriet/hjelmsamlingen, hvilket kunne beskadige tryktætningspakningen, motorhjelmen og/eller ventilhusets ID, samt skabe sammensatte problemer og ineffektivitet, som damplækage kan have på anlæggets drift. Som et resultat tog Valve-designere flere skridt for at løse dette problem.
Figur 2 viser en kombination af spændingsfyldte motorhjelmoptagningsbolte (derved opretholder en konstant belastning på pakningen, minimerer risikoen for lækage) og udskiftningen af jern/blødt stål, forsølvet tryktætningspakning med en, der er lavet af matrice- dannet grafit. Pakningsdesignet vist i figur 3 kan installeres i tryktætningsventiler, der tidligere er leveret med den traditionelle type pakning. Fremkomsten af grafitpakninger har yderligere styrket pålideligheden og ydeevnen af tryktætningsventilen i de fleste applikationer og til selv daglige start/stop-driftscyklusser.
Selvom mange producenter stadig anbefaler "hot torquing", er potentialet for lækage, når dette ikke er gjort, stærkt formindsket. Siddefladerne i tryktætningsventiler, som i mange kraftværksventiler, udsættes for relativt høje sædebelastninger. Sædets integritet opretholdes som en funktion af snævre bearbejdningstolerancer på komponentdele, midler til at give det nødvendige drejningsmoment til at åbne/lukke som en funktion af gear eller aktivering, og valg/påføring af passende materialer til siddeoverflader.
Kobolt-, nikkel- og jernbaserede hardfacing-legeringer anvendes til optimal slidstyrke af kile-/skive- og sæderingens sædeoverflader. Mest almindeligt anvendte er CoCr-A (f.eks. Stellite) materialer. Disse materialer påføres med en række forskellige processer, herunder afskærmet metalbue, gasmetalbue, gaswolframbue og plasma (overført) bue. Mange tryktætninger Globe Valves er designet med integrerede hardfacede sæder, mens portventilen og kontraventilerne typisk har hardfacede sæderinge, der er svejset ind i ventilhuset.
Ventilende terminologi
Hvis du har beskæftiget dig med ventilering i længere tid, har du sikkert bemærket, at ventilproducenter ikke er alt for kreative med de termer og sprogbrug, der bruges i branchen. Tag for eksempel "boltede motorhjelmventiler." Kroppen er boltet til motorhjelmen for at opretholde systemets integritet. For "tryktætningsventiler" hjælper systemets tryk tætningsmekanismen. For "stop/kontrolventiler", når ventilspindelen er i lukket position, stoppes flowet mekanisk, men når det er i åben position, er skiven fri til at handle for at kontrollere en vending af flowet. Det samme princip gælder for anden terminologi, der bruges til design, såvel som ventiltyper og deres komponenter.
Indlægstid: 11. maj 2020