Anzugsdrehmoment
Um eine leckagefreie Flanschverbindung zu erhalten, ist eine ordnungsgemäße Installation der Dichtungen erforderlich, die Schrauben müssen auf die richtige Schraubenspannung eingestellt werden und die Gesamtkraft der Schrauben muss gleichmäßig über die gesamte Flanschfläche verteilt sein.
Mit Drehmomentanzug (Aufbringen einer Vorspannung auf ein Befestigungselement durch Drehen der Mutter des Befestigungselements) kann die richtige Schraubenspannung erreicht werden.
Das richtige Anziehen einer Schraube bedeutet, die elastischen Eigenschaften der Schraube optimal zu nutzen. Um gut zu funktionieren, muss sich ein Bolzen wie eine Feder verhalten. Im Betrieb übt der Anzugsvorgang eine axiale Vorspannung auf die Schraube aus. Diese Zugbelastung ist natürlich gleich und entgegengesetzt zur Druckkraft, die auf die zusammengebauten Komponenten ausgeübt wird. Sie kann als „Anziehlast“ oder „Zuglast“ bezeichnet werden.

www.enerpac.com
Drehmomentschlüssel
Drehmomentschlüssel ist die allgemeine Bezeichnung für ein handgeführtes Schraubwerkzeug und dient dazu, die Kraft einer Verbindung wie einer Mutter oder eines Bolzens präzise einzustellen. Es ermöglicht dem Bediener, die auf die Schraube ausgeübte Rotationskraft (Drehmoment) zu messen, um sie an die Spezifikationen anzupassen.

Manueller und hydraulischer Schraubenschlüssel
Die Auswahl der richtigen Befestigungstechnik für Flanschschrauben erfordert Erfahrung. Die erfolgreiche Anwendung einer Technik erfordert auch die Qualifikation sowohl der verwendeten Werkzeuge als auch der Mannschaft, die die Arbeit verrichtet. Im Folgenden sind die am häufigsten verwendeten Techniken zum Anziehen von Flanschschrauben zusammengefasst.
- Manueller Schraubenschlüssel
- Schlagschrauber
- Hammerschlüssel
- Hydraulischer Drehmomentschlüssel
- Manueller Drehmomentschlüssel mit Balken- und Getriebeunterstützung
- Hydraulischer Schraubenspanner
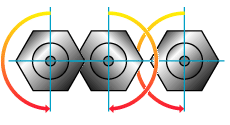
Drehmomentverlust
Bei jeder Schraubverbindung kommt es zwangsläufig zu einem Drehmomentverlust. Die kombinierten Auswirkungen von Schraubenentspannung (ungefähr 10 % während der ersten 24 Stunden nach der Installation), Kriechen der Dichtung, Vibrationen im System, Wärmeausdehnung und elastische Wechselwirkung beim Anziehen der Schrauben tragen zum Drehmomentverlust bei. Wenn der Drehmomentverlust ein Extrem erreicht, übersteigt der Innendruck die Druckkraft, die die Dichtung an Ort und Stelle hält, und es kommt zu einer Undichtigkeit oder einem Platzen.
Ein Schlüssel zur Reduzierung dieser Auswirkungen ist die ordnungsgemäße Installation der Dichtung. Durch das langsame und parallele Zusammenführen der Flansche beim Einbau einer Dichtung und das Durchführen von mindestens vier Schraubenanziehdurchgängen unter Beachtung der richtigen Schraubenanziehreihenfolge ergeben sich geringere Wartungskosten und eine erhöhte Sicherheit.
Auch die richtige Dicke der Dichtung ist wichtig. Je dicker die Dichtung ist, desto größer ist das Kriechen der Dichtung, was wiederum zu einem Drehmomentverlust führen kann. Bei standardmäßigen ASME-Flanschen mit erhöhter Fläche wird normalerweise eine 1,6 mm dicke Dichtung empfohlen. Dünnere Dichtungsmaterialien können eine höhere Dichtungslast und damit höhere Innendrücke aushalten.
Schmierung verringert die Reibung
Durch die Schmierung wird die Reibung beim Anziehen verringert, das Versagen der Schrauben während der Installation verringert und die Lebensdauer der Schrauben erhöht. Schwankungen der Reibungskoeffizienten wirken sich auf die Höhe der Vorspannung aus, die bei einem bestimmten Drehmoment erreicht wird. Höhere Reibung führt zu einer geringeren Umwandlung von Drehmoment in Vorspannung. Um den erforderlichen Drehmomentwert genau ermitteln zu können, muss der vom Schmiermittelhersteller angegebene Wert für den Reibungskoeffizienten bekannt sein.
Sowohl auf die Auflagefläche der Mutter als auch auf die Außengewinde sollten Schmiermittel oder Mittel gegen Festfressen aufgetragen werden.
Anzugsreihenfolge
Im ersten Durchgang ziehen Sie die erste Schraube leicht an, bewegen Sie sie dann direkt quer oder um 180 Grad für die zweite Schraube, bewegen Sie sie dann um eine Vierteldrehung um den Kreis oder um 90 Grad für die dritte Schraube und direkt quer für die vierte. Setzen Sie diese Reihenfolge fort, bis alle Schrauben festgezogen sind.
Verwenden Sie beim Anziehen eines Vier-Schrauben-Flansches ein Kreuzmuster.
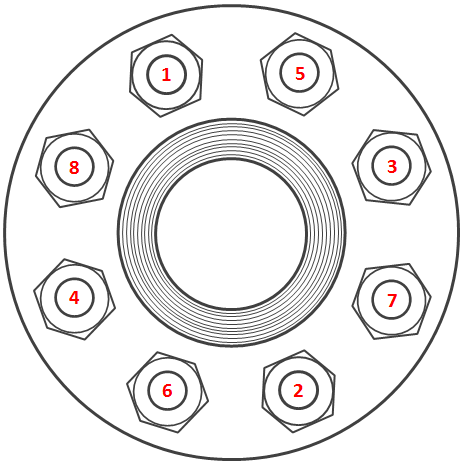
Vorbereitung der Flanschverschraubung
Bei einer Flanschverbindung müssen alle Bauteile stimmen, um eine Abdichtung zu erreichen. Die häufigste Ursache für undichte Dichtungsverbindungen sind unsachgemäße Installationsverfahren.
Bevor mit dem Verschraubungsprozess begonnen wird, können die folgenden vorbereitenden Schritte zukünftige Probleme vermeiden:
- Reinigen Sie die Flanschflächen und prüfen Sie sie auf Narben. Die Flächen müssen sauber und frei von Mängeln (Grate, Grübchen, Dellen usw.) sein.
- Überprüfen Sie alle Schrauben und Muttern visuell auf beschädigte oder korrodierte Gewinde. Ersetzen oder reparieren Sie Schrauben oder Muttern nach Bedarf.
- Alle Gewinde entgraten.
- Schmieren Sie das Gewinde der Schraube oder des Bolzens sowie die Oberfläche der Mutterfläche neben dem Flansch oder der Unterlegscheibe. Für die meisten Anwendungen werden gehärtete Unterlegscheiben empfohlen.
- Installieren Sie die neue Dichtung und stellen Sie sicher, dass die Dichtung richtig zentriert ist. Alte Dichtungen NICHT WIEDERVERWENDEN und auch MEHRERE Dichtungen verwenden.
- Überprüfen Sie die Flanschausrichtung ASME B31.3 Prozessrohrleitungen:
…Flanschflächen müssen innerhalb von 1/16 Zoll pro Fuß Durchmesser parallel sein und Flanschschraubenlöcher müssen mit einem maximalen Versatz von 1/8 Zoll ausgerichtet sein. - Passen Sie die Position der Muttern so an, dass 2–3 Gewindegänge über der Oberkante der Mutter sichtbar sind.
Unabhängig davon, welche Befestigungsmethode verwendet wird, müssen immer die oben genannten Prüfungen und Vorbereitungen durchgeführt werden.
Anmerkung(en) des Autors…
Meine eigenen Erfahrungen mit … Drehmomentschlüsseln
- In der Vergangenheit habe ich Hunderte leckagefreie Flanschverbindungen montiert, von NPS 1/2 bis NPS 24 und größer. Ich habe daher selten einen Drehmomentschlüssel verwendet.
In der Praxis werden „normale“ Rohrflanschverbindungen fast nie mit einem Drehmomentschlüssel montiert. Die schwierigsten Verbindungen waren für mich immer die „Kleinen“ und dann insbesondere der Raised-Face-Typ über Klasse 300 (RF-Höhe = ca. 6,4 mm).
Die Flanschflächen eines NPS 1/2-Flansches sind beispielsweise kleiner als beispielsweise bei einem NPS 6-Flansch, und die Wahrscheinlichkeit einer Fehlausrichtung ist meiner Meinung nach viel größer.
In der Praxis stoße ich regelmäßig auf Flanschverbindungen, bei denen die Ausrichtung nicht im Toleranzbereich liegt. Wenn einfach die Reihenfolge des Anzugsverfahrens befolgt wird, ist der Mechaniker nicht gut beschäftigt. Eventuell muss am Bolzen sechs statt am Bolzen eins begonnen werden. Achten Sie bei der Flanschmontage auf Ihre Augen, das ist sehr wichtig und trägt höchstwahrscheinlich zu einer leckagefreien Verbindung bei
Falsche Flanschverbindungen – die Schrauben sind zu kurz!
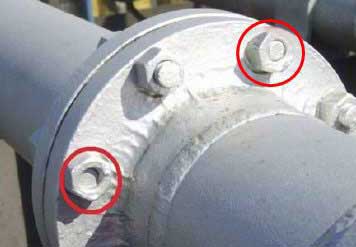
Was können Sie tun?
- Das Bild zeigt einen falsch verschraubten Flansch, da zwei Schrauben zu kurz sind und die Muttern nicht vollständig auf den Schrauben sitzen. Dies bedeutet, dass das Gelenk möglicherweise nicht so stark ist, wie es sein sollte. Flansche sind so konstruiert, dass die gesamte Mutter-Schrauben-Kombination die auf den Flansch einwirkenden Kräfte aufnimmt. Wenn die Mutter nur teilweise auf die Schraube aufgeschraubt ist, ist die Verbindung möglicherweise nicht stark genug.
- Wenn Ihre Arbeit den Zusammenbau von Geräten, die Montage von Flanschrohren, das Verschrauben von Schachtdeckeln oder anderen Schraubverbindungen an Geräten oder die Montage anderer Geräte umfasst, denken Sie daran, dass die Arbeit erst dann abgeschlossen ist, wenn alle Schrauben ordnungsgemäß installiert und festgezogen sind.
- Für einige Geräte sind spezielle Verfahren zum Anziehen der Schrauben erforderlich. Beispielsweise müssen Sie möglicherweise einen Drehmomentschlüssel verwenden, um die Schrauben gemäß der Spezifikation korrekt anzuziehen, oder die Schrauben in einer speziellen Reihenfolge anziehen. Stellen Sie sicher, dass Sie das richtige Verfahren befolgen, die richtigen Werkzeuge verwenden und dass Sie in der Vorgehensweise bei der Gerätemontage ordnungsgemäß geschult sind.
- Überprüfen Sie im Rahmen Ihrer Anlagensicherheitsinspektionen Rohre und Geräte auf ordnungsgemäß verschraubte Flansche. Zur einfachen Orientierung: Schrauben, die nicht über die Muttern hinausragen, sollten von einem Rohrleitungsbauer oder Ingenieur überprüft werden.
- Wenn Sie in Ihrer Anlage falsch verschraubte Flansche feststellen, melden Sie diese, damit sie repariert werden können, und stellen Sie sicher, dass die erforderlichen Reparaturen durchgeführt werden.
- Überprüfen Sie neue Geräte oder Geräte, die nach der Wartung wieder zusammengebaut wurden, um sicherzustellen, dass sie vor der Inbetriebnahme richtig zusammengebaut und richtig verschraubt sind.
Was ist die richtige Länge eines Stehbolzens?
Als Regel können Sie Folgendes verwenden: Der freie Gewindegang der Schraube über der Oberkante der Mutter entspricht 1/3 des Schraubendurchmessers.
Zeitpunkt der Veröffentlichung: 04.08.2020