Introduction aux vannes à joint de pression
Vannes à joint de pression
La construction avec joint de pression est adoptée pour les vannes destinées à un service à haute pression, généralement supérieure à 170 bars. La caractéristique unique du joint de pression du chapeau est que l'étanchéité des joints corps-chapeau s'améliore à mesure que la pression interne dans la vanne augmente, par rapport à d'autres constructions où l'augmentation de la pression interne a tendance à créer des fuites dans le joint corps-chapeau.
Conception de joint de pression
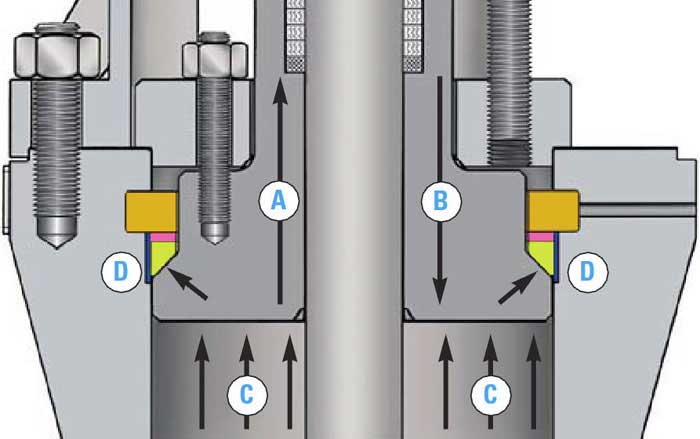
- A/B – Tendance du capot à monter ou descendre lorsque la pression change
- C – Pression du système
- D – Forces d’étanchéité dues à la pression
Plus la pression interne est élevée, plus la force d’étanchéité est grande. Un démontage facile est rendu possible en laissant tomber l'ensemble capot dans la cavité du corps et en chassant les anneaux de poussée à quatre segments au moyen d'une goupille poussoir.
S'appuyant sur des principes de conception assez simples, les vannes à joint de pression ont prouvé leur capacité à gérer des applications de plus en plus exigeantes d'isolation de vapeur fossile et à cycle combiné, alors que les concepteurs continuent de repousser les enveloppes de pression/température des chaudières, des HRSG et des systèmes de tuyauterie. Les vannes à joint de pression sont généralement disponibles dans des tailles allant de 2 pouces à 24 pouces et dans des classes de pression ASME B16.34 allant de #600 à #2500, bien que certains fabricants puissent répondre au besoin de diamètres plus grands et de valeurs nominales plus élevées pour des applications spéciales.
Les vannes à joint de pression sont disponibles dans de nombreuses qualités de matériaux telles que A105 forgé et moulé Gr.WCB, alliage F22 forgé et moulé Gr.WC9 ; F11 forgé et fonte Gr.WC6, acier inoxydable austénitique F316 forgé et fonte Gr.CF8M ; pour des températures supérieures à 500°C, nuances forgées F316H et fontes austénitiques adaptées.
Le concept de conception des joints sous pression remonte au milieu des années 1900, lorsque, confrontés à des pressions et des températures toujours croissantes (principalement dans les applications de puissance), les fabricants de vannes ont commencé à concevoir des alternatives à l'approche traditionnelle du chapeau boulonné pour sceller le joint corps/chapeau. . En plus de fournir un niveau plus élevé d'intégrité d'étanchéité de l'enceinte de pression, de nombreuses conceptions de vannes à joint de pression pesaient nettement moins que leurs homologues de vannes à chapeau boulonnées.
Chapeaux boulonnés vs joints à pression
Pour mieux comprendre le concept de conception des joints sous pression, comparons le mécanisme d'étanchéité corps-chapeau entre les chapeaux boulonnés et les joints sous pression.Figure 1représente la vanne à chapeau boulonné typique. La bride du corps et la bride du chapeau sont reliées par des goujons et des écrous, avec un joint de conception/matériau approprié inséré entre les faces de la bride pour faciliter l'étanchéité. Les goujons/écrous/boulons sont serrés aux couples prescrits selon un modèle défini par le fabricant pour assurer une étanchéité optimale. Cependant, à mesure que la pression du système augmente, le risque de fuite à travers le joint corps/capot augmente également.
Examinons maintenant le joint d'étanchéité à pression détaillé dansFigure 2Notez les différences dans les configurations respectives des articulations corps/capot. La plupart des conceptions de joints à pression intègrent des « boulons de fixation du capot » pour tirer le capot vers le haut et le sceller contre le joint d'étanchéité à pression. Cela crée à son tour un joint entre le joint et le diamètre intérieur (ID) du corps de la vanne.


Un anneau de poussée segmenté maintient la charge. La beauté de la conception du joint de pression réside dans le fait qu'à mesure que la pression du système augmente, la charge sur le chapeau et, par conséquent, le joint d'étanchéité de pression augmente également. Par conséquent, dans les vannes à joint sous pression, à mesure que la pression du système augmente, le risque de fuite à travers le joint corps/chapeau diminue.
Cette approche de conception présente des avantages distincts par rapport aux vannes à chapeau boulonnées dans les systèmes principaux de vapeur, d'eau d'alimentation, de dérivation de turbine et d'autres systèmes de centrales électriques nécessitant des vannes capables de relever les défis inhérents aux applications à haute pression et température.
Mais au fil des années, à mesure que les pressions/températures de fonctionnement augmentaient et avec l'avènement des usines de pointe, cette même pression transitoire du système qui aidait à l'étanchéité a également fait des ravages dans l'intégrité des joints d'étanchéité sous pression.
Joints d'étanchéité à pression
L'un des principaux composants impliqués dans l'étanchéité de la vanne d'étanchéité à pression est le joint lui-même. Les premiers joints d'étanchéité à pression étaient fabriqués en fer ou en acier doux. Ces joints ont ensuite été plaqués argent pour profiter de la capacité du matériau de placage plus souple à fournir une étanchéité plus serrée. En raison de la pression appliquée lors de l'hydrotest de la vanne, un « jeu » (ou déformation du profil du joint) entre le chapeau et le joint a été constaté. En raison de l'élasticité inhérente du boulon de reprise du capot et de l'élasticité du joint d'étanchéité à la pression, il existait un risque que le capot bouge et casse cet « ensemble » lorsqu'il est soumis à des augmentations/diminutions de pression du système, avec pour conséquence une fuite du joint corps/capot.
Ce problème pourrait être efficacement résolu en utilisant la pratique consistant à « serrer à chaud » les boulons de fixation du capot après l'égalisation de la pression et de la température du système, mais cela nécessitait que le personnel de maintenance du propriétaire/utilisateur le fasse après le démarrage de l'usine. Si cette pratique n'était pas respectée, il existait un risque de fuite à travers le joint corps/chapeau, ce qui pourrait endommager le joint d'étanchéité à pression, le chapeau et/ou le diamètre intérieur du corps de la vanne, ainsi que créer des problèmes aggravés et des inefficacités que le les fuites de vapeur pourraient avoir sur le fonctionnement de l'usine. En conséquence, les concepteurs de Valve ont pris plusieurs mesures pour résoudre ce problème.
La figure 2 montre une combinaison de boulons de fixation du chapeau soumis à une forte charge (maintenant ainsi une charge constante sur le joint, minimisant le risque de fuite) et le remplacement du joint d'étanchéité à pression plaqué argent en fer/acier doux par un joint en métal moulé. graphite formé. La conception du joint illustrée à la figure 3 peut être installée dans des vannes à joint sous pression précédemment fournies avec le joint de type traditionnel. L'avènement des joints en graphite a encore renforcé la fiabilité et les performances de la vanne à joint de pression dans la plupart des applications et même pour les cycles de fonctionnement marche/arrêt quotidiens.
Bien que de nombreux fabricants recommandent encore le « serrage à chaud », le risque de fuite lorsque cela n'est pas effectué est considérablement réduit. Les surfaces d'appui des vannes à joint de pression, comme dans de nombreuses vannes de centrales électriques, sont soumises à des charges d'appui relativement élevées. L'intégrité du siège est maintenue en fonction de tolérances d'usinage serrées sur les composants, de moyens permettant de fournir le couple requis pour l'ouverture/fermeture en fonction des engrenages ou de l'actionnement, et de la sélection/application de matériaux appropriés pour les surfaces d'assise.
Des alliages de rechargement dur à base de cobalt, de nickel et de fer sont utilisés pour une résistance à l'usure optimale des surfaces d'appui du coin/disque et de la bague de siège. Les matériaux CoCr-A (par exemple Stellite) sont les plus couramment utilisés. Ces matériaux sont appliqués avec une variété de procédés, notamment l'arc métallique blindé, l'arc gazeux métallique, l'arc gazeux au tungstène et l'arc plasma (transféré). De nombreux robinets à soupape à joint de pression sont conçus avec des sièges intégrés à surface dure, tandis que les robinets-vannes et les clapets anti-retour ont généralement des anneaux de siège à surface dure qui sont soudés dans le corps de la vanne.
Terminologie des vannes
Si vous travaillez dans le domaine des vannes depuis un certain temps, vous avez probablement remarqué que les fabricants de vannes ne sont pas trop créatifs avec les termes et la langue vernaculaire utilisés dans le secteur. Prenons par exemple les « vannes à chapeau boulonnées ». La carrosserie est boulonnée au capot pour maintenir l'intégrité du système. Pour les «vannes à joint sous pression», la pression du système facilite le mécanisme d'étanchéité. Pour les « clapets d'arrêt/retour », lorsque la tige de la vanne est en position fermée, le débit est arrêté mécaniquement, mais lorsqu'elle est en position ouverte, le disque est libre d'agir pour vérifier une inversion du débit. Ce même principe s'applique à d'autres termes utilisés pour la conception, ainsi qu'aux types de vannes et à leurs composants.
Heure de publication : 11 mai 2020