Acabado de cara de brida
Acabado de cara de brida
O código ASME B16.5 require que a cara da brida (cara elevada e cara plana) teña unha rugosidade específica para garantir que esta superficie sexa compatible coa xunta e proporcione un selado de alta calidade.
Requírese un acabado dentado, concéntrico ou en espiral, con 30 a 55 ranuras por polgada e unha rugosidade resultante entre 125 e 500 micro polgadas. Isto permite que os fabricantes de bridas dispoñan de varios graos de acabado superficial para a superficie de contacto das xuntas das bridas metálicas.
A imaxe mostra un acabado dentado nunha cara elevada.
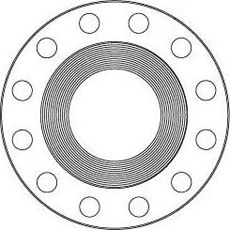
As superficies máis utilizadas
Acabado Stock
O máis utilizado de calquera acabado de superficie de brida, porque practicamente, é axeitado para todas as condicións de servizo común. Baixo compresión, a cara branda dunha xunta incorporarase neste acabado, o que axuda a crear un selado e xérase un alto nivel de fricción entre as superficies de acoplamento.
O acabado destas bridas é xerado por unha ferramenta de nariz redonda de radio de 1,6 mm cunha velocidade de avance de 0,8 mm por revolución ata 12 polgadas. Para tamaños de 14 polgadas ou máis, o acabado realízase cunha ferramenta de punta redonda de 3,2 mm cunha alimentación de 1,2 mm por revolución.
Serrado en espiral
Este tamén é un suco en espiral continuo ou fonográfica, pero difiere do acabado original en que o suco normalmente xérase mediante unha ferramenta de 90° que crea unha xeometría en "V" cun dentado en ángulo de 45°.
Serrado concéntrico
Como o nome indica, este acabado está composto por sucos concéntricos. Utilízase unha ferramenta de 90° e os dentados están espazados uniformemente pola cara.
Acabado liso
Este acabado non mostra marcas de ferramenta visualmente aparentes. Estes acabados utilízanse normalmente para xuntas con revestimentos metálicos, como dobre revestimento, aceiro plano e metal corrugado. As superficies lisas únense para crear un selado e dependen da planitude das caras opostas para realizar un selado. Normalmente, isto conséguese tendo a superficie de contacto da xunta formada por unha ranura espiral continua (ás veces chamada fonográfica) xerada por unha ferramenta de punta redonda de 0,8 mm de radio a unha velocidade de avance de 0,3 mm por revolución cunha profundidade de 0,05 mm. Isto dará lugar a unha rugosidade entre Ra 3,2 e 6,3 micrómetros (125 - 250 micro polgadas).

Comentario(s) do autor...
ACABADO LISO
É adecuado para xunta espiral e xunta non metálica?
Para que tipo de aplicación é este tipo?
As preguntas anteriores fanse moitas veces. Intento dar unha resposta correcta.
As bridas de acabado liso son máis comúns para conducións de baixa presión e/ou de gran diámetro e están destinadas principalmente ao seu uso con xuntas de metal sólido ou enroladas en espiral.
Os acabados lisos adoitan atoparse en maquinaria ou xuntas con bridas que non sexan as bridas de tubos. Cando se traballa cun acabado liso, é importante considerar o uso dunha xunta máis fina para diminuír os efectos do fluído e do fluxo frío. Con todo, hai que ter en conta que tanto unha xunta máis delgada como o acabado liso, por si só, requiren unha maior forza de compresión (é dicir, un par de parafuso) para conseguir o selado.
Quizais teña visto este comentario:
Mecanizado das caras de xuntas das bridas ata un acabado liso de Ra = 3,2 – 6,3 micrómetros
(= 125 – 250 micropolgadasAARH)
AARHé a altura de rugosidade media aritmética. Utilízase para medir a rugosidade (máis ben a suavidade) das superficies. 125AARHsignifica que 125 micro polgadas será a altura media das subidas e baixadas da superficie.
63 AARHse especifica para xuntas tipo anel.
125-250AARH(chámase acabado liso) especifícase para xuntas de ferida en espiral.
250-500AARH(denomínase acabado en stock) especifícase para xuntas brandas como NON amianto, láminas de grafito, elastómeros, etc. Se usamos un acabado liso para xuntas brandas non se producirá o suficiente "efecto mordedor" e, polo tanto, a xunta pode desenvolver fugas.
Ás vecesAARHtamén se refire comoRaque significa Rugosidade Media e significa o mesmo.
Hora de publicación: 06-07-2020