プレッシャーシールバルブの紹介
プレッシャーシールバルブ
圧力シール構造は、通常 170 bar を超える高圧サービス用のバルブに採用されています。圧力シールボンネットのユニークな特徴は、内圧の増加により本体とボンネットの接合部に漏れが発生しやすい他の構造と比較して、バルブの内圧が増加すると本体とボンネットの接合部のシールが向上することです。
圧力シール設計
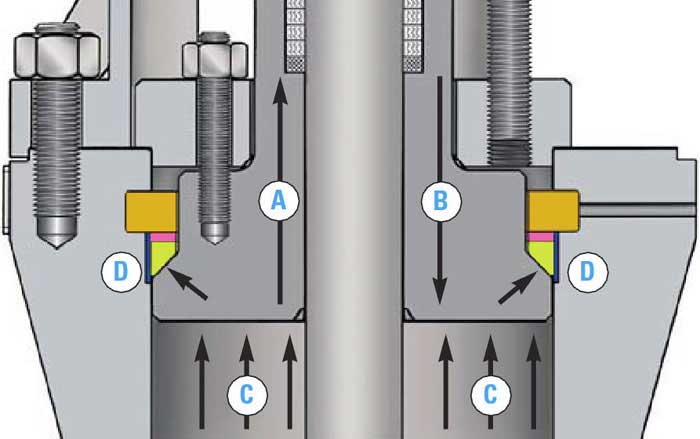
- A/B – 圧力の変化に応じてボンネットが上下する傾向
- C – システム圧力
- D – 圧力によるシール力
内圧が高いほどシール力は大きくなります。ボンネットAssyをボディキャビティに落とし込み、4分割スラストリングを押しピンで打ち抜くだけで簡単に分解できます。
圧力シールバルブは、設計者がボイラー、HRSG、および配管システムの圧力/温度エンベロープの要求を継続的に追求する中で、非常にシンプルな設計原則に基づいて、ますます要求の厳しい化石燃料および複合サイクル蒸気隔離用途に対応できる能力を実証してきました。圧力シール バルブは、通常、2 インチから 24 インチのサイズ範囲と、#600 から #2500 の ASME B16.34 圧力クラスで入手可能ですが、一部のメーカーは特殊な用途でのより大きな直径とより高い定格のニーズに対応できます。
圧力シール バルブは、A105 鍛造および Gr.WCB 鋳造、合金 F22 鍛造および Gr.WC9 鋳造など、多くの材質で入手可能です。 F11 鍛造および Gr.WC6 鋳造、オーステナイト系ステンレス F316 鍛造および Gr.CF8M 鋳造。 500°C 以上の場合は、F316H 鍛造および適切なオーステナイト鋳造グレード。
圧力シールの設計コンセプトは 1900 年代半ばまで遡ることができます。当時、バルブ メーカーは(主に電力用途で)増え続ける圧力と温度に直面して、ボディとボンネットの接合部をシールする従来のボルト締めボンネット アプローチに代わるものを設計し始めました。 。圧力境界シールの完全性をより高いレベルで提供することに加えて、圧力シール バルブ設計の多くは、ボルト締めされたボンネット バルブに比べて重量が大幅に軽減されました。
ボルト締めボンネット vs. 圧力シール
圧力シールの設計概念をよりよく理解するために、ボルトで締められたボンネットと圧力シールの間のボディとボンネット間のシール機構を対比してみましょう。図1典型的なボルト付きボンネット バルブを示しています。ボディフランジとボンネットフランジはスタッドとナットによって結合され、シールを容易にするためにフランジ面の間に適切な設計/材料のガスケットが挿入されます。スタッド/ナット/ボルトは、最適なシールを実現するために、メーカーが定義したパターンで規定のトルクで締め付けられます。ただし、システム圧力が増加すると、ボディ/ボンネット接合部からの漏れの可能性も増加します。
次に、圧力シールジョイントの詳細を見てみましょう。図2ボディ/ボンネットそれぞれの接合部形状の違いに注意してください。ほとんどの圧力シール設計には、ボンネットを引き上げて圧力シール ガスケットをシールする「ボンネット テイクアップ ボルト」が組み込まれています。これにより、ガスケットとバルブ本体の内径 (ID) の間にシールが形成されます。


分割されたスラストリングが負荷を維持します。圧力シール設計の利点は、システムの圧力が増加すると、ボンネットへの負荷も増加し、それに応じて圧力シール ガスケットへの負荷も増加することです。したがって、圧力シールバルブでは、システム圧力が増加するにつれて、ボディ/ボンネット接合部からの漏れの可能性が減少します。
この設計アプローチは、主蒸気、給水、タービンバイパス、および高圧および高温用途に固有の課題に対処できるバルブを必要とするその他の発電所システムにおいて、ボルト留めボンネットバルブに比べて明確な利点があります。
しかし、長年にわたって動作圧力/温度が上昇し、ピーキングプラントの出現に伴い、シールに役立っていたこの同じ一時的なシステム圧力も、圧力シール接合部の完全性に大きな影響を及ぼしました。
プレッシャーシールガスケット
圧力シールバルブのシールに関与する主要コンポーネントの 1 つはガスケット自体です。初期の圧力シール ガスケットは鉄または軟鋼で製造されていました。その後、これらのガスケットは銀メッキされ、より柔らかいめっき材料がより堅固なシールを提供する能力を利用しました。バルブの水圧試験中に加えられた圧力により、ボンネットとガスケットの間に「セット」(またはガスケットプロファイルの変形)が生じました。ボンネットのテークアップ ボルトと圧力シールの接合部に固有の弾性があるため、システム圧力の増減にさらされるとボンネットが移動してその「セット」が壊れる可能性があり、その結果、ボディ/ボンネットの接合部に漏れが発生します。
この問題は、システムの圧力と温度を均一化した後にボンネットの巻き取りボルトを「ホットトルク」する方法を利用することで効果的に解消できますが、プラントの起動後に所有者/ユーザーの保守担当者がこれを行う必要がありました。この慣行が遵守されていない場合、本体とボンネットの接合部から漏れが発生する可能性があり、圧力シール ガスケット、ボンネット、および/またはバルブ本体の ID が損傷する可能性があり、また、複合的な問題や非効率が生じる可能性があります。蒸気漏れが発生すると、工場の操業に影響を及ぼす可能性があります。その結果、Valve の設計者はこの問題に対処するためにいくつかの措置を講じました。
図 2 は、活荷重がかかっているボンネットのテークアップ ボルト (ガスケットに一定の荷重を維持し、漏れの可能性を最小限に抑える) と、鉄/軟鋼の銀メッキ圧力シール ガスケットを金型製のものに置き換えたものを示しています。形成されたグラファイト。図 3 に示すガスケット設計は、従来のタイプのガスケットが付属していた圧力シール バルブに取り付けることができます。グラファイト ガスケットの出現により、ほとんどの用途および毎日の開始/停止動作サイクルにおいても、圧力シール バルブの信頼性と性能がさらに強化されました。
多くのメーカーは依然として「ホットトルク」を推奨していますが、これを行わない場合でも漏れの可能性は大幅に減少します。圧力シールバルブの座面は、多くの発電所のバルブと同様に、比較的高い座面荷重にさらされます。シートの完全性は、構成部品の厳しい機械加工公差、ギアまたは作動の機能として開閉に必要なトルクを提供する手段、およびシート表面に適切な材料を選択/適用することによって維持されます。
コバルト、ニッケル、鉄ベースの硬化肉盛合金は、ウェッジ/ディスクとシート リングの座面の耐摩耗性を最適化するために利用されています。最も一般的に使用されるのは、CoCr-A (ステライトなど) 材料です。これらの材料は、シールド金属アーク、ガス金属アーク、ガスタングステン アーク、プラズマ (転写) アークなどのさまざまなプロセスで適用されます。多くの圧力シール グローブ バルブは一体型硬化処理シートを備えて設計されていますが、ゲート バルブとチェック バルブは通常、バルブ本体に溶接された硬化処理シート リングを備えています。
バルブの用語
バルブにある程度の期間取り組んだことがある人なら、バルブのメーカーがビジネスで使用される用語や専門用語に対してあまり創造的ではないことにおそらく気づいているでしょう。たとえば、「ボルト締めボンネットバルブ」を考えてみましょう。システムの完全性を維持するために、ボディはボンネットにボルトで固定されています。 「圧力シールバルブ」の場合、システム圧力がシール機構を補助します。 「ストップ/チェックバルブ」の場合、バルブステムが閉位置にある場合、流れは機械的に停止されますが、開位置にある場合、ディスクは自由に動作して流れの逆転をチェックします。これと同じ原則が、バルブのタイプとその構成部品だけでなく、設計に使用される他の用語にも当てはまります。
投稿日時: 2020 年 5 月 11 日