압력 씰 밸브 소개
압력 씰 밸브
일반적으로 170bar를 초과하는 고압 서비스용 밸브에는 압력 씰 구조가 채택됩니다. 압력 씰 보닛의 독특한 특징은 내부 압력의 증가로 인해 바디-보닛 조인트에서 누출이 발생하는 경향이 있는 다른 구조에 비해 밸브의 내부 압력이 증가함에 따라 바디-보닛 조인트 씰이 향상된다는 것입니다.
압력 밀봉 설계
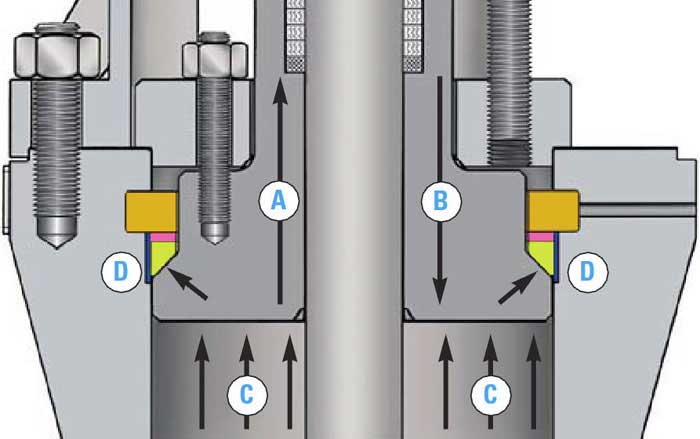
- A/B – 압력 변화에 따라 보닛이 위 또는 아래로 움직이는 경향
- C – 시스템 압력
- D – 압력으로 인한 밀봉력
내부 압력이 높을수록 밀봉력이 커집니다. 보닛 어셈블리를 본체 구멍에 떨어뜨리고 푸시 핀을 사용해 4분할 스러스트 링을 밀어내면 쉽게 분해할 수 있습니다.
설계자가 보일러, HRSG 및 배관 시스템 압력/온도 한계를 계속해서 밀어붙이면서 상당히 단순한 설계 원리에 기초한 압력 씰 밸브는 점점 더 까다로워지는 화석 연료 및 복합 사이클 증기 분리 응용 분야를 처리할 수 있는 능력을 입증했습니다. 압력 씰 밸브는 일반적으로 2인치~24인치의 크기 범위와 #600~#2500의 ASME B16.34 압력 등급으로 제공되지만 일부 제조업체에서는 특수 용도에 대해 더 큰 직경과 더 높은 등급에 대한 요구를 수용할 수 있습니다.
압력 밀봉 밸브는 A105 단조 및 Gr.WCB 주조, 합금 F22 단조 및 Gr.WC9 주조와 같은 다양한 재료 품질로 제공됩니다. F11 단조 및 Gr.WC6 주조, 오스테나이트계 스테인리스 F316 단조 및 Gr.CF8M 주조; 500°C 이상의 온도에서는 F316H 단조 및 적합한 오스테나이트 주조 등급입니다.
압력 씰 설계 개념은 1900년대 중반으로 거슬러 올라갑니다. 당시 밸브 제조업체는 점점 증가하는 압력과 온도(주로 전력 응용 분야)에 직면하여 본체/보닛 조인트를 밀봉하기 위한 기존의 볼트 보닛 접근 방식에 대한 대안을 설계하기 시작했습니다. . 더 높은 수준의 압력 경계 밀봉 무결성을 제공하는 동시에 많은 압력 밀봉 밸브 설계의 무게는 볼트로 연결된 보닛 밸브에 비해 훨씬 가볍습니다.
볼트형 보닛과 압력 씰 비교
압력 씰 설계 개념을 더 잘 이해하기 위해 볼트로 고정된 보닛과 압력 씰 사이의 몸체와 보닛 사이의 씰링 메커니즘을 대조해 보겠습니다.그림 1전형적인 Bolted Bonnet 밸브를 묘사합니다. 본체 플랜지와 보닛 플랜지는 스터드와 너트로 결합되며, 씰링을 용이하게 하기 위해 플랜지 면 사이에 적절한 디자인/재질의 개스킷이 삽입됩니다. 스터드/너트/볼트는 최적의 밀봉에 영향을 미치기 위해 제조업체가 정의한 패턴에 따라 규정된 토크로 조여집니다. 그러나 시스템 압력이 증가함에 따라 본체/보닛 조인트를 통한 누출 가능성도 증가합니다.
이제 에 자세히 설명된 압력 밀봉 조인트를 살펴보겠습니다.그림 2각 본체/보닛 조인트 구성의 차이점을 확인하세요. 대부분의 압력 밀봉 설계에는 "보닛 테이크업 볼트"가 포함되어 보닛을 위로 당겨 압력 밀봉 개스킷에 대해 밀봉합니다. 그러면 개스킷과 밸브 본체의 내부 직경(ID) 사이에 밀봉이 생성됩니다.


분할된 스러스트 링이 하중을 유지합니다. 압력 밀봉 설계의 장점은 시스템 압력이 증가함에 따라 보닛과 이에 따라 압력 밀봉 개스킷에 가해지는 부하도 커진다는 것입니다. 따라서 압력 밀봉 밸브에서는 시스템 압력이 증가함에 따라 본체/보닛 조인트를 통한 누출 가능성이 감소합니다.
이 설계 접근 방식은 주 증기, 급수, 터빈 바이패스 및 고압 및 온도 응용 분야에 내재된 문제를 처리할 수 있는 밸브가 필요한 기타 발전소 시스템에서 볼트 체결식 보닛 밸브에 비해 뚜렷한 이점을 제공합니다.
그러나 수년에 걸쳐 작동 압력/온도가 증가하고 피크 플랜트의 출현으로 밀봉에 도움이 되는 동일한 일시적인 시스템 압력은 압력 밀봉 조인트 무결성에 큰 피해를 입혔습니다.
압력 씰 개스킷
압력 밀봉 밸브를 밀봉하는 데 관련된 주요 구성 요소 중 하나는 개스킷 자체입니다. 초기 압력 밀봉 개스킷은 철 또는 연강으로 제조되었습니다. 이 개스킷은 더 단단한 밀봉을 제공하는 더 부드러운 도금 재료의 능력을 활용하기 위해 이후에 은도금되었습니다. 밸브의 수압 테스트 중에 적용된 압력으로 인해 보닛과 개스킷 사이에 "설정"(또는 개스킷 프로필의 변형)이 발생했습니다. 고유한 보닛 테이크업 볼트와 압력 밀봉 조인트 탄성으로 인해 시스템 압력 증가/감소에 따라 보닛이 움직이고 해당 "설정"이 파손될 가능성이 존재했으며, 이로 인해 본체/보닛 조인트 누출이 발생했습니다.
이 문제는 시스템 압력 및 온도 균등화 후 보닛 테이크업 볼트에 "뜨거운 토크"를 적용하는 방식을 활용하여 효과적으로 해결할 수 있지만, 공장 가동 후에는 소유자/사용자 유지보수 담당자가 이를 수행해야 했습니다. 이 관행을 준수하지 않으면 본체/보닛 조인트를 통한 누출 가능성이 존재하여 압력 밀봉 개스킷, 보닛 및/또는 밸브 본체의 ID가 손상될 수 있을 뿐만 아니라 복합적인 문제와 비효율성을 초래할 수 있습니다. 증기 누출은 공장 운영에 영향을 미칠 수 있습니다. 결과적으로 Valve 설계자들은 이 문제를 해결하기 위해 몇 가지 조치를 취했습니다.
그림 2는 활하중 보닛 테이크업 볼트(따라서 개스킷에 일정한 부하를 유지하여 누출 가능성을 최소화)의 조합과 철/연강, 은도금 압력 밀봉 개스킷을 다이로 만든 것으로 교체한 것을 보여줍니다. 흑연을 형성했습니다. 그림 3에 표시된 개스킷 설계는 이전에 기존 유형의 개스킷과 함께 공급된 압력 밀봉 밸브에 설치할 수 있습니다. 흑연 개스킷의 출현으로 대부분의 응용 분야는 물론 일일 시작/중지 작동 주기에서도 압력 밀봉 밸브의 신뢰성과 성능이 더욱 확고해졌습니다.
많은 제조업체가 여전히 "열간 토크"를 권장하지만 이를 수행하지 않을 경우 누출 가능성은 크게 줄어듭니다. 많은 발전소 밸브와 마찬가지로 압력 밀봉 밸브의 시트 표면은 상대적으로 매우 높은 시트 하중을 받습니다. 시트 무결성은 구성 부품의 엄격한 가공 공차, 기어 또는 작동 기능으로 열거나 닫는 데 필요한 토크를 제공하는 수단, 시트 표면에 적합한 재료를 선택/적용하는 기능으로 유지됩니다.
웨지/디스크 및 시트 링 시트 표면의 최적의 내마모성을 위해 코발트, 니켈 및 철 기반 표면 경화 합금이 활용됩니다. 가장 일반적으로 사용되는 것은 CoCr-A(예: Stellite) 재료입니다. 이들 재료는 차폐 금속 아크, 가스 금속 아크, 가스 텅스텐 아크, 플라즈마(이송) 아크 등 다양한 공정에 적용됩니다. 많은 압력 밀봉 글로브 밸브는 일체형 하드페이스 시트를 갖도록 설계되는 반면, 게이트 밸브 및 체크 밸브는 일반적으로 밸브 본체에 용접되는 하드페이스 시트 링을 갖습니다.
밸브 용어
오랫동안 밸브 관련 작업을 해보신 분이라면 밸브 제조업체가 비즈니스에 사용되는 용어와 언어에 지나치게 창의적이지 않다는 점을 눈치채셨을 것입니다. 예를 들어 "볼트형 보닛 밸브"를 생각해 보십시오. 본체는 시스템 무결성을 유지하기 위해 보닛에 볼트로 고정되어 있습니다. "압력 밀봉 밸브"의 경우 시스템 압력이 밀봉 메커니즘을 보조합니다. "정지/체크 밸브"의 경우 밸브 스템이 닫힌 위치에 있으면 흐름이 기계적으로 중지되지만 열린 위치에 있으면 디스크가 자유롭게 작동하여 흐름의 역전을 확인합니다. 이와 동일한 원칙은 설계에 사용되는 다른 용어는 물론 밸브 유형 및 해당 구성 부품에도 적용됩니다.
게시 시간: 2020년 5월 11일