Wprowadzenie do zaworów z uszczelnieniem ciśnieniowym
Zawory z uszczelnieniem ciśnieniowym
Konstrukcja uszczelnienia ciśnieniowego jest przystosowana do zaworów pracujących pod wysokim ciśnieniem, zwykle powyżej 170 barów. Unikalną cechą uszczelki ciśnieniowej Bonnet jest to, że uszczelnienie połączeń korpus-maska poprawia się wraz ze wzrostem ciśnienia wewnętrznego w zaworze, w porównaniu z innymi konstrukcjami, w których wzrost ciśnienia wewnętrznego ma tendencję do powodowania nieszczelności w połączeniu korpus-maska.
Konstrukcja uszczelnienia ciśnieniowego
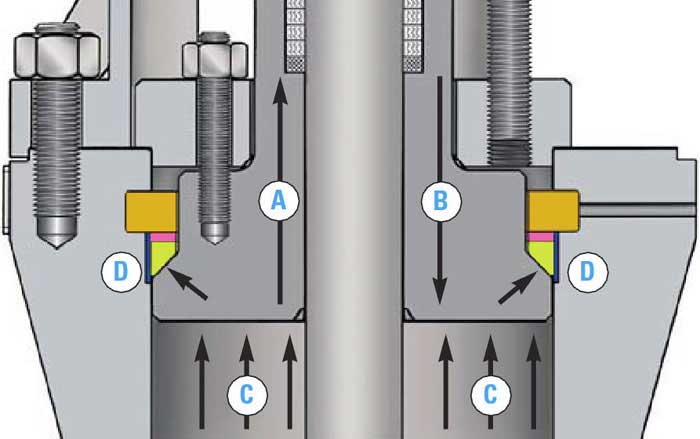
- A/B – tendencja maski do przesuwania się w górę lub w dół wraz ze zmianą ciśnienia
- C – Ciśnienie w układzie
- D – Siły uszczelniające pod wpływem ciśnienia
Im wyższe ciśnienie wewnętrzne, tym większa siła uszczelniająca. Łatwy demontaż jest możliwy poprzez wrzucenie zespołu maski do wnęki korpusu i wybicie czterosegmentowych pierścieni oporowych za pomocą sworznia.
Opierając się na dość prostych zasadach konstrukcyjnych, zawory z uszczelnieniem ciśnieniowym udowodniły swoją zdolność do radzenia sobie z coraz bardziej wymagającymi zastosowaniami w izolacji pary z paliw kopalnych i w cyklu kombinowanym, ponieważ projektanci nadal naciskają na koperty ciśnieniowo-temperaturowe w kotłach, HRSG i systemach rurociągów. Zawory z uszczelnieniem ciśnieniowym są zazwyczaj dostępne w zakresie rozmiarów od 2 cali do 24 cali i klasach ciśnienia ASME B16.34 od #600 do #2500, chociaż niektórzy producenci mogą uwzględnić zapotrzebowanie na większe średnice i wyższe wartości znamionowe do zastosowań specjalnych.
Zawory z uszczelnieniem ciśnieniowym są dostępne w wykonaniu z wielu materiałów, takich jak kute A105 i odlewy Gr.WCB, kute stopy F22 i odlewy Gr.WC9; Kuta F11 i odlew Gr.WC6, stal austenityczna F316 kuta i odlew Gr.CF8M; dla ponad 500°C, kute F316H i odpowiednie gatunki odlewów austenitycznych.
Koncepcja projektowania uszczelnień ciśnieniowych sięga połowy XX wieku, kiedy w obliczu stale rosnących ciśnień i temperatur (głównie w zastosowaniach energetycznych) producenci zaworów zaczęli projektować alternatywy dla tradycyjnego podejścia do uszczelniania połączenia korpusu z pokrywą przykręcaną śrubą . Oprócz zapewnienia wyższego poziomu integralności uszczelnienia granicy ciśnienia, wiele konstrukcji zaworów z uszczelnieniem ciśnieniowym ważyło znacznie mniej niż ich przykręcane odpowiedniki z zaworami pokrywowymi.
Przykręcane maski a uszczelki ciśnieniowe
Aby lepiej zrozumieć koncepcję konstrukcyjną uszczelnienia ciśnieniowego, porównajmy mechanizm uszczelniający korpus-maska pomiędzy przykręcanymi śrubami pokrywami i uszczelkami ciśnieniowymi.Ryc. 1przedstawia typowy zawór z przykręcaną pokrywą. Kołnierz korpusu i kołnierz maski są połączone za pomocą śrub dwustronnych i nakrętek, a pomiędzy powierzchniami kołnierzy znajduje się uszczelka o odpowiedniej konstrukcji/materiału, aby ułatwić uszczelnienie. Kołki/nakrętki/śruby są dokręcane zalecanym momentem obrotowym według wzoru określonego przez producenta, aby zapewnić optymalne uszczelnienie. Jednakże wraz ze wzrostem ciśnienia w układzie zwiększa się również ryzyko wycieku przez złącze korpus/maska.
Przyjrzyjmy się teraz szczegółowo złączu z uszczelką ciśnieniowąRyc. 2Należy zwrócić uwagę na różnice w odpowiednich konfiguracjach połączeń nadwozia/maski. Większość konstrukcji uszczelnień ciśnieniowych zawiera „śruby mocujące pokrywę”, które podciągają pokrywę do góry i uszczelniają uszczelkę ciśnieniową. To z kolei tworzy uszczelnienie pomiędzy uszczelką a wewnętrzną średnicą (ID) korpusu zaworu.


Segmentowy pierścień oporowy utrzymuje obciążenie. Piękno konstrukcji uszczelnienia ciśnieniowego polega na tym, że wraz ze wzrostem ciśnienia w układzie rośnie obciążenie maski i, odpowiednio, uszczelki ciśnieniowej. Dlatego w przypadku zaworów z uszczelnieniem ciśnieniowym wraz ze wzrostem ciśnienia w układzie zmniejsza się ryzyko wycieku przez połączenie korpus/pokrywa.
To podejście projektowe ma wyraźne zalety w porównaniu z przykręcanymi zaworami pokrywowymi w głównej parze, wodzie zasilającej, obejściu turbiny i innych systemach elektrowni wymagających zaworów, które poradzą sobie z wyzwaniami nieodłącznie związanymi z zastosowaniami wysokociśnieniowymi i temperaturowymi.
Jednak z biegiem lat, wraz ze wzrostem ciśnienia/temperatury roboczej i pojawieniem się instalacji osiągających szczytowe wartości, to samo przejściowe ciśnienie w systemie, które pomagało w uszczelnianiu, spowodowało również spustoszenie w integralności złącza z uszczelnieniem ciśnieniowym.
Uszczelki ciśnieniowe
Jednym z głównych elementów uszczelniających zawór ciśnieniowy jest sama uszczelka. Wczesne uszczelki ciśnieniowe były produkowane z żelaza lub miękkiej stali. Uszczelki te zostały następnie posrebrzone, aby wykorzystać zdolność bardziej miękkiego materiału powlekającego do zapewnienia mocniejszego uszczelnienia. Ze względu na ciśnienie wywierane podczas hydrotestu zaworu, stwierdzono „zestawienie” (lub odkształcenie profilu uszczelki) pomiędzy pokrywą a uszczelką. Ze względu na nieodłączną elastyczność śruby mocującej pokrywy silnika i uszczelki dociskowej, istniała możliwość przesunięcia się maski i złamania tego „zestawu” pod wpływem wzrostu/spadku ciśnienia w układzie, co skutkowało nieszczelnością złącza korpusu/maski.
Problemowi temu można skutecznie zaradzić, stosując praktykę „dokręcania na gorąco” śrub mocujących pokrywę silnika po wyrównaniu ciśnienia i temperatury w układzie, ale wymagało to wykonania tej czynności przez personel konserwacyjny właściciela/użytkownika po uruchomieniu instalacji. W przypadku nieprzestrzegania tej praktyki istniałoby ryzyko wycieku przez złącze korpusu/pokrywy, co mogłoby uszkodzić uszczelkę ciśnieniową, pokrywę i/lub identyfikator korpusu zaworu, a także powodować problemy i nieefektywność, które wyciek pary mógłby mieć wpływ na funkcjonowanie zakładu. W rezultacie projektanci Valve podjęli kilka kroków, aby rozwiązać ten problem.
Rysunek 2 przedstawia kombinację śrub podnoszących pokrywę obciążonych pod obciążeniem (w ten sposób utrzymując stałe obciążenie uszczelki, minimalizując ryzyko wycieku) i wymianę uszczelki ciśnieniowej z żelaza/miękkiej stali, posrebrzanej na uszczelkę wykonaną z matrycy uformowany grafit. Konstrukcja uszczelki pokazana na rysunku 3 może być instalowana w zaworach z uszczelnieniem ciśnieniowym, które były wcześniej dostarczane z uszczelką tradycyjnego typu. Pojawienie się uszczelek grafitowych jeszcze bardziej wzmocniło niezawodność i wydajność zaworu z uszczelnieniem ciśnieniowym w większości zastosowań, nawet w codziennych cyklach uruchamiania/zatrzymywania.
Chociaż wielu producentów nadal zaleca „dokręcanie na gorąco”, ryzyko wycieku, jeśli nie jest to wykonywane, jest znacznie zmniejszone. Powierzchnie uszczelniające zaworów z uszczelnieniem ciśnieniowym, podobnie jak w wielu zaworach elektrowni, są poddawane, mówiąc porównywalnie, bardzo dużym obciążeniom uszczelniającym. Integralność gniazda jest utrzymywana w zależności od wąskich tolerancji obróbki części składowych, sposobów zapewnienia wymaganego momentu obrotowego do otwierania/zamykania w zależności od przekładni lub napędu oraz doboru/zastosowania odpowiednich materiałów na powierzchnie gniazd.
Aby zapewnić optymalną odporność na zużycie powierzchni uszczelniających klina/tarczy i pierścienia gniazda, stosuje się stopy do napawania na bazie kobaltu, niklu i żelaza. Najczęściej stosowane są materiały CoCr-A (np. Stellite). Materiały te są nakładane różnymi procesami, w tym łukiem metalowym w osłonie, łukiem gazowo-metalowym, łukiem gazowo-wolframowym i łukiem plazmowym (przenoszonym). Wiele zaworów kulowych z uszczelnieniem ciśnieniowym ma zintegrowane, utwardzane gniazda, podczas gdy zasuwy i zawory zwrotne mają zazwyczaj utwardzane pierścienie gniazdowe, które są przyspawane do korpusu zaworu.
Terminologia dotycząca zaworów
Jeśli zajmujesz się zaworami od dłuższego czasu, prawdopodobnie zauważyłeś, że producenci zaworów nie są zbyt kreatywni, jeśli chodzi o terminy i język używany w branży. Weźmy na przykład „przykręcane zawory maski”. Korpus jest przykręcony do maski, aby zachować integralność systemu. W przypadku „zaworów z uszczelnieniem ciśnieniowym” ciśnienie w układzie wspomaga mechanizm uszczelniający. W przypadku „zaworów odcinających/zwrotnych”, gdy trzpień zaworu znajduje się w pozycji zamkniętej, przepływ jest zatrzymywany mechanicznie, natomiast w pozycji otwartej dysk może swobodnie działać, sprawdzając odwrócenie przepływu. Ta sama zasada dotyczy innej terminologii stosowanej w projektowaniu, a także typów zaworów i ich części składowych.
Czas publikacji: 11 maja 2020 r