Introduktion till trycktätningsventiler
Trycktätningsventiler
Trycktätningskonstruktionen används för ventiler för högtrycksservice, vanligtvis över 170 bar. Den unika egenskapen med trycktätningens motorhuv är att kropp-huv-skarvarnas tätningar förbättras när det interna trycket i ventilen ökar, jämfört med andra konstruktioner där ökningen av inre tryck tenderar att skapa läckor i kropp-huv-leden.
Trycktätningsdesign
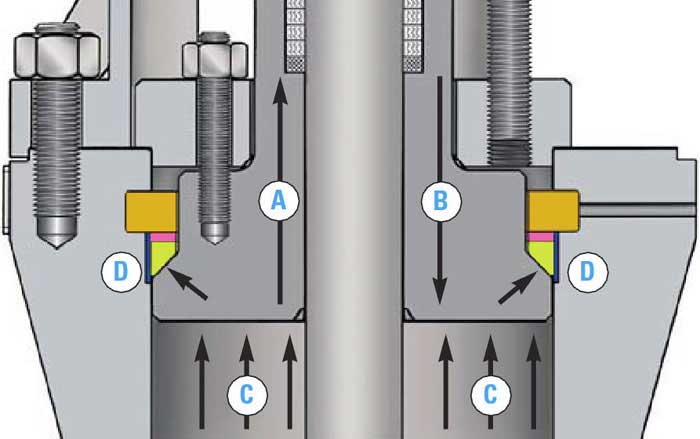
- A/B – Motorhuvens tendens att röra sig uppåt eller nedåt när trycket ändras
- C – Systemtryck
- D – Tätningskrafter på grund av tryck
Ju högre inre tryck, desto större tätningskraft. Enkel demontering är möjlig genom att släppa motorhuvsenheten i kroppshåligheten och driva ut de fyra segmenterade tryckringarna med hjälp av en tryckstift.
Tack vare ganska enkla konstruktionsprinciper har trycktätningsventiler bevisat sin förmåga att hantera allt mer krävande fossila och kombinerade ångisoleringsapplikationer, eftersom konstruktörer fortsätter att trycka på panna, HRSG och rörsystem tryck/temperatur. Trycktätningsventiler är vanligtvis tillgängliga i storleksintervall från 2 tum till 24 tum och ASME B16.34 tryckklasser från #600 till #2500, även om vissa tillverkare kan tillgodose behovet av större diametrar och högre klassificeringar för speciella applikationer.
Trycktätningsventiler finns i många materialkvaliteter såsom A105 smidda och Gr.WCB gjutna, legering F22 smidda och Gr.WC9 gjutna; F11 smidd och Gr.WC6 gjuten, austenitisk rostfri F316 smidd och Gr.CF8M gjuten; för över 500°C, F316H smidda och lämpliga austenitiska gjutkvaliteter.
Designkonceptet med trycktätningar kan spåras tillbaka till mitten av 1900-talet, då ventiltillverkare inför ständigt ökande tryck och temperaturer (främst i krafttillämpningar) började designa alternativ till den traditionella metoden med skruvad motorhuv för att täta kopplingen mellan kropp och motorhuv. . Tillsammans med att tillhandahålla en högre nivå av tryckgränstätningsintegritet vägde många av trycktätningsventilkonstruktionerna betydligt mindre än deras bultade motorhuvsventilmotsvarigheter.
Bultade motorhuvar vs. trycktätningar
För att bättre förstå konceptet med trycktätningsdesign, låt oss kontrastera tätningsmekanismen mellan kropp och motorhuv mellan bultade motorhuvar och trycktätningar.Fig. 1föreställer den typiska Bolted Bonnet-ventilen. Kroppens fläns och motorhuvsflänsen är förenade med bultar och muttrar, med en packning av lämplig design/material insatt mellan flänsytorna för att underlätta tätningen. Dubbar/muttrar/bultar dras åt med föreskrivna vridmoment i ett mönster definierat av tillverkaren för att påverka optimal tätning. Men när systemtrycket ökar, ökar också risken för läckage genom kroppen/huvens leden.
Låt oss nu titta på trycktätningsfogen som beskrivs i detaljFig. 2Notera skillnaderna i respektive konfigurationer för kaross/motorhuv. De flesta trycktätningskonstruktioner innehåller "Bunnet take-up bolts" för att dra upp motorhuven och täta mot trycktätningspackningen. Detta skapar i sin tur en tätning mellan packningen och ventilhusets innerdiameter (ID).


En segmenterad tryckring upprätthåller belastningen. Det fina med trycktätningsdesignen är att när systemtrycket ökar, ökar också belastningen på motorhuven och, på motsvarande sätt, trycktätningspackningen. Därför, i trycktätningsventiler, när systemtrycket ökar, minskar risken för läckage genom kopplingen mellan kropp och motorhuv.
Denna designstrategi har tydliga fördelar jämfört med bultade motorhuvsventiler i huvudånga, matarvatten, turbinbypass och andra kraftverkssystem som kräver ventiler som kan hantera utmaningarna i högtrycks- och temperaturapplikationer.
Men under årens lopp, allt eftersom drifttrycket/temperaturerna ökade, och med tillkomsten av toppanläggningar, har samma transienta systemtryck som hjälpte till förseglingen också förstört trycktätningsfogens integritet.
Trycktätningspackningar
En av de primära komponenterna som är involverade i tätningen av trycktätningsventilen är själva packningen. Tidiga trycktätningspackningar tillverkades av järn eller mjukt stål. Dessa packningar silverpläterades sedan för att dra fördel av det mjukare pläteringsmaterialets förmåga att ge en tätare tätning. På grund av trycket som applicerades under ventilens hydrotest, togs en "set" (eller deformation av packningsprofilen) mellan motorhuven och packningen. På grund av den inneboende motorhuvens upptagningsbult och trycktätningsfogens elasticitet, fanns potentialen för motorhuven att röra sig och gå sönder den "härdade" när den utsätts för systemtrycksökningar/-minskningar, vilket resulterade i läckage av kaross/huvsfog.
Detta problem skulle effektivt kunna elimineras genom att använda praxisen att "varma vridmoment" på motorhuvens upptagningsbultar efter systemtryck och temperaturutjämning, men det krävde att ägaren/användarens underhållspersonal gjorde det efter att anläggningen startat. Om denna praxis inte följdes, fanns risken för läckage genom kopplingen mellan kropp/huv, vilket skulle kunna skada trycktätningspackningen, ventilhuset och/eller ID:n på ventilkroppen, samt skapa sammansättningsproblem och ineffektivitet som ångläckage kan ha på anläggningens drift. Som ett resultat tog ventildesigners flera steg för att lösa detta problem.
Figur 2 visar en kombination av spänningssatta motorhuvsupptagningsbultar (sålunda bibehåller en konstant belastning på packningen, vilket minimerar risken för läckage) och bytet av järn/mjukt stål, silverpläterad trycktätningspackning med en gjord av form- bildat grafit. Packningsdesignen som visas i figur 3 kan installeras i trycktätningsventiler som tidigare levererats med den traditionella typen av packning. Tillkomsten av grafitpackningar har ytterligare förstärkt pålitligheten och prestandan hos trycktätningsventilen i de flesta applikationer och även för dagliga start/stopp-driftcykler.
Även om många tillverkare fortfarande rekommenderar "hot torquing", minskar potentialen för läckage när detta inte görs avsevärt. Sätesytorna i trycktätning Ventiler, som i många kraftverk Ventiler, utsätts för jämförelsevis mycket höga sätesbelastningar. Sätets integritet bibehålls som en funktion av snäva bearbetningstoleranser på komponentdelar, sätt att tillhandahålla det erforderliga vridmomentet för att öppna/stänga som en funktion av växlar eller aktivering, och val/applicering av lämpliga material för sittytor.
Kobolt-, nickel- och järnbaserade hårdbeläggningslegeringar används för optimal slitstyrka på kilen/skivan och sätesringens sitsytor. Mest vanligt använda är CoCr-A (t.ex. Stellite)-material. Dessa material appliceras med en mängd olika processer, inklusive skärmad metallbåge, gasmetallbåge, gasvolframbåge och plasma (överförd) båge. Många trycktätningsglobventiler är designade med inbyggda hårda säten, medan grindventilen och backventilerna vanligtvis har hårda sätesringar som är svetsade in i ventilkroppen.
Valving terminologi
Om du har sysslat med ventiler under en längre tid, har du förmodligen märkt att ventiltillverkare inte är alltför kreativa med termerna och det språk som används i verksamheten. Ta till exempel "bultade motorhuvsventiler". Kroppen är bultad till motorhuven för att bibehålla systemets integritet. För "trycktätningsventiler" underlättar systemets tryck tätningsmekanismen. För "stopp/kontrollventiler", när ventilskaftet är i stängt läge, stoppas flödet mekaniskt, men när det är i öppet läge är skivan fri att agera för att kontrollera en omkastning av flödet. Samma princip gäller för annan terminologi som används för design, såväl som ventiltyper och deras beståndsdelar.
Posttid: 11 maj 2020